Workers’ Compensation rates for the meat industry remain significantly higher in every state in Australia when compared to other industries (Australian Meat Processor Corporation, 2018). Swickers is a large abattoir and meat processing facility located in Kingaroy, Queensland, approximately three hours’ drive north-west of Brisbane. Coming into 2018 the site recognized there was a significant problem. Injury rates and associated costs were climbing, along with a high turnover of staff. All this was despite having a costly onsite health provider that spruced a revolutionary system for managing soft tissue injuries.
Fast forward to June, 2019, and Swickers has reversed the market injury trend and achieved extraordinary improvements in injury rates, compensation claim numbers and associated costs. Specifically, the site was able to achieve the following:
- 51% reduction in sprain and strain injuries
- 59% reduction in sprain and strain costs
- 73% reduction in paid days (days when a worker is being paid by the Workers’ Compensation insurer)
- Turnover during probation decreasing 25%
- Total turnover decreasing by 50%
How was this able to be achieved?
Through adopting a proactive risk-based framework that cross-references physical demands of the work with the physical capacity of the workforce.
This overall risk approach is outlined by the following diagram:
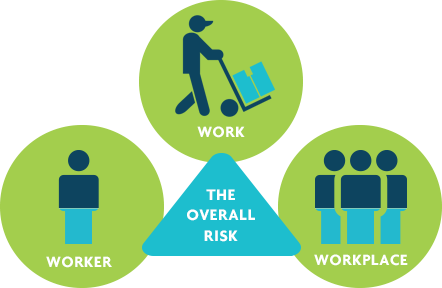
At a site level this fundamental shift in managing musculoskeletal health and physical demands of the work required buy in from senior leadership and all department sectors. The belief that proactive input was paramount had to be taken on board. No longer could Swickers afford to not be proactively risk managing their people and jobs.
Online data management systems are utilised to communicate objectively with all key stakeholders across the business. This brings to life the risk management system in real time, enabling for proactive matching of jobs to workers, and workers to jobs.
There has also been a fundamental shift in thinking for the site regarding their people, which moves to acknowledge people as long-term assets that are worth investing in. Swickers are committed to investing in the physical capacity of their people, and to matching them to appropriate work.
The site has also taken positive steps towards understanding the task-based manual risk profile of the site. This is being achieved through a process of consultative and participative ergonomic programs, with high level engineering and automation-based control projects being undertaken. Swickers have taken the first steps toward truly proactive workplace health and are now reaping the benefits of the market-leading decision making.
References:
AMPC, 2018. Available from: https://www.ampc.com.au/uploads/cgblog/id418/Appendix_C_for_Milestone_7_Final_report_V2-Reduced_051218.pdf